PCS-print Pre-inking System
PCS-print pre-inking system reads the digital file from the digital printing workflow, analyses the separation color data and figure out the ink thickness of ink zones automatically, pushes the information into Remote Ink Control System, then finished the presetting activities before print.
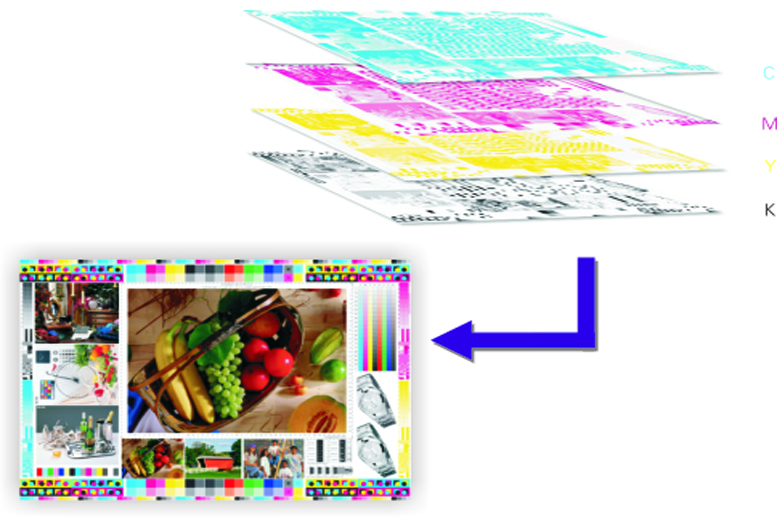
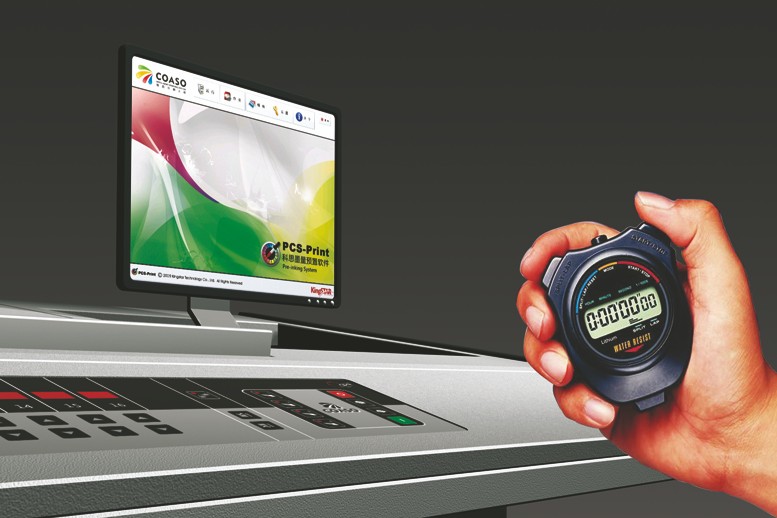
Main Features
- Rapidly and accurately create template
The characteristic document of printing has considered many factors including ink, papers, environment, machine and so on. The internal data transform is based on printing standard testing layout. It can be easily loaded to the template, and then make sure that we can set up the template rapidly and accurately.
- Properly designed software, and rapidly data process
Using the guide to create the job, and choose the proper template. The users can easily edit or amend the Job. The whole process is easy to master.
- Presetting data is transmitted to press through network
Running a job, open the ppf File, system will figure out key values automatically
and transmit it to remote ink control system. Whole process is so easy and simple.
Wasting materials and timeswill be solved immediately
Lower reject rate
Stable color quality
Short print preparing time
Well ink uniformity
Reduce spoil
Reduce the waste of ink
PCS-Print pre-inking system not only can match with KICS remote ink control system, but also can access to the press ofHeidelberg, Manroland, Goebel, KOMORI, Mitsubishi, RYOBI, Akiyama, sakurai etc
Besides 4 primary inks, the PCS-Print system also can control up to 16 spot inks. Meanwhile, user can get the conversion between dot area and ink amount according to the practice printing, and extend the application scope of pre-inking.
The pre-inking system comes with CIP3/CIP4 interface, direc-tly receives the ink layout information of statistical distribution fr-om prepress. It is instead of scanning the plates, improving the production efficiency.
By using the prepress system, we can get the presetting data easily and avoid many errors caused by scanning, so the accur-acy is guaranteed
The system can calculate the thickness data ranged over the layout less than one minute, data accuracy achieves 85%, whi-ch greatly simplifies the process.